THE ROLE OF RESISTORS IN POWERING ICEBREAKERS
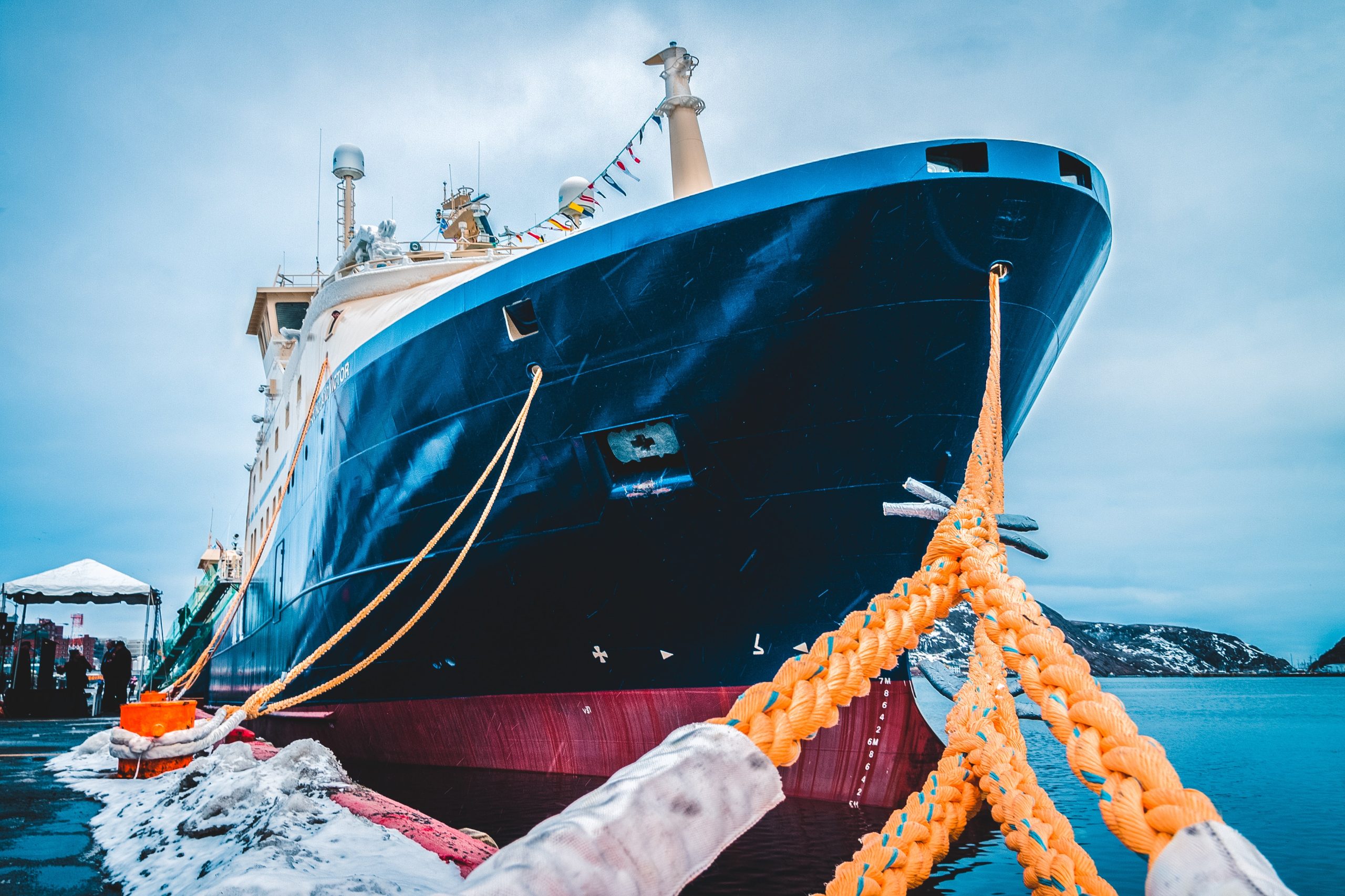
Sea ice covers around twelve per cent of the world’s oceans, blocking the path for ships attempting to travel across the Earth’s coldest regions. Although they aren’t a new concept, icebreaker ships consistently play a crucial role in clearing these routes for trade, research projects and travel.
Icebreaker ships are a special class of vessel designed to break through even the thickest of ice sheets. Initially developed to open up trade routes that experience either seasonal or permanent ice conditions, ice breakers are commonly found in areas like the Barents Sea, Artic Ocean and the Saint Lawrence Seaway. More recently, they’ve also been used to support scientific research projects in the Arctic and Antarctic.
DETAILED DESIGN
To meet the challenges of ice-covered waters, icebreaker ships have a very specific, carefully considered design. The bow of an icebreaker has a unique shape that is smoother and rounder than a standard vessel, to allow it to easily glide over thick ice sheets with minimal opposing force. As it glides over the ice in this way, the weight of the ship descends onto the ice, crushing it and clearing the path.
To power the icebreakers to smoothly move over this difficult seascape, the vessels also require a significantly enhanced electric propulsion system that matches the power requirements for the icebreaker’s thrusters to break through the ice.
As the sole enabler of transportation through these ice-covered waters, it’s essential that the propulsion system — and all of the components that it includes — are reliable, effective and safeguarded. If an icebreaker were to fail in transit, there could be major disruption to the global supply chain in the repair time. Think the Suez Canal fiasco in 2021, but much colder.
RELIABLE RESISTORS
One component that plays a crucial role in ensuring the safe operation of an icebreaker’s electric propulsion system is a dynamic braking resistor (DBR). When there is no ice in the vessel’s path, there’s less load on the system, meaning that any excess energy produced is surplus to requirements. To dissipate this excess energy, a DBR is integrated into the system, which acts as a load dump during propulsion and icebreaking activities. This load dump activity stabilises the power system, giving a constant load to the vessel’s gas engines.
It’s important to include a DBR in the electric drive system of an icebreaker for several reasons. Without the DBR, the power system would destabilise, risking potential damage to other components of the power circuit. If this continued, it could eventually lead to the loss of the vessel’s icebreaking function and complete failure of the power system.
Therefore, integrating a DBR is an absolute essential for icebreaker vessel design engineers. However, it’s not as simple as just selecting a DBR. There are several design elements for this specific application that must be considered to ensure the drive’s optimal performance.
MARINE MATTERS
When designing electrical components, like resistors, for use on icebreakers, there are several application-specific factors to consider. Each component needs to be able to withstand the salty, cold and unstable conditions that are common at sea.
In terms of structural stability, conducting rigorous testing procedures like finite element analysis (FEA) provides evidence of a component’s ability to withstand unpredictable, inhospitable conditions. It’s also important to design in line with standards outlined by the global testing, inspection and certification specialists Bureau Veritas, for global compliance.
The saline atmosphere at sea is corrosive, so selecting the right material is essential to prevent salty sea water from leaving equipment inoperable. For metal components, it’s important to use stainless steel with a chromium content of at least 10.5 per cent. This enables the stainless steel to react with oxygen to produce a protective layer that prevent corrosion, even in an unpainted condition.
Icebreaker vessels are an indispensable part of the marine transport system. While their function is simple, having the right electrical components, including DBRs, designed specifically for icebreaking applications, is crucial to their safe and successful operation, making even the most treacherous of routes in the Polar regions accessible all year round.
Cressall designs and manufactures DBRs specifically for icebreaker vessels. Our team of expert engineers works together with our customers to develop the ideal, customer DBR solution for each application. For more information, please get in touch here.