CLEANING UP AUTOMOTIVE EMISSIONS
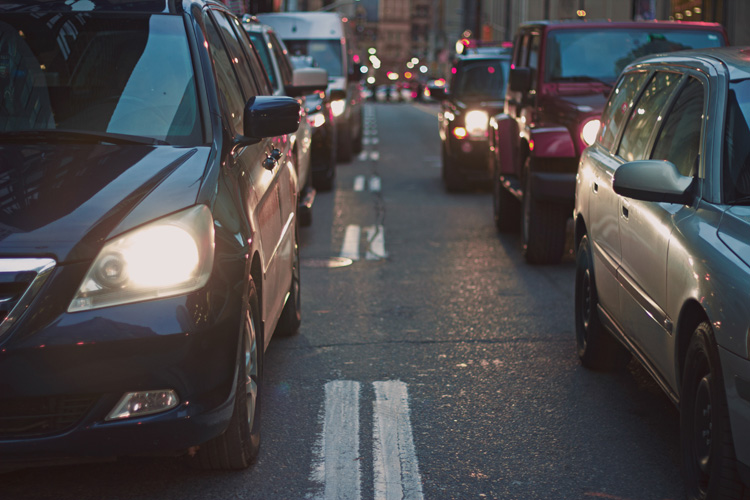
IT’S TIME TO START ADDRESSING NON-EXHAUST EMMISSIONS
Road transportation is widely recognised as a large contributor to carbon emissions, responsible for 24 per cent of the global total. However, carbon isn’t the only thing the world’s vehicle fleet emits —non-exhaust emissions also have a detrimental impact on the health of the population and the planet.
Electric vehicles (EVs) are often referred to as ‘zero emission’, but this is not entirely true since non-exhaust emissions are produced by all vehicles, irrespective of their fuel source. In fact, the EV rollout is not expected to have any impact on non-exhaust emissions.
IT’S NOT JUST CO2
Non-exhaust emissions are particles released from brake, tyre and road surface wear, resulting in the production of particulate matter — all chemical compounds and materials in the air that are not gas. Particulate matter is classified depending on the diameter of the particles. PM10 and PM2.5 refer to particles less than ten micrometres and 2.5 micrometres in diameter.
Particulate matter from non-exhaust emissions originates from surface wear, which leads to abrasion and the release of small particles that become airborne. Friction between brake pads and the rotating disc and between the tyre and the road both lead to abrasion, component wear and the release of particles from the surfaces into the atmosphere.
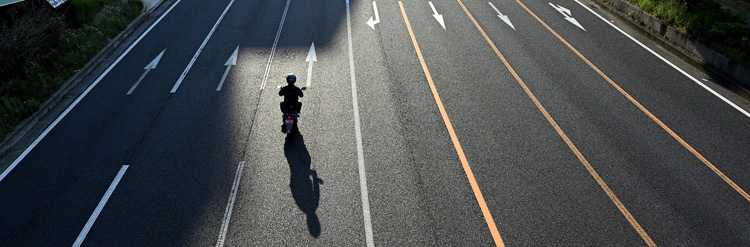
THE PROBLEM WITH PARTICULATE MATTER
The minute size of these particles means that some of the toxins that they include are small enough to enter the human body through the bloodstream, where they can cause serious damage to the heart, brain and respiratory systems. According to the World Health Organisation (WHO), nine out of ten people worldwide breathe polluted air, and seven million people die a year because of the health effects of air pollution.
In addition to the detrimental effects on human health, particulate matter can seriously damage the environment. Once airborne, it can be carried large distances and settle on the ground or in water where toxins can lead to catastrophic ecosystem disruption, altering the nutrients of water and soil and contributing to increased acidity and agricultural destruction.
With so many issues, it comes as a surprise that several nations lack a policy regulating non-exhaust emissions. The current legal limit for PM2.5 is 25 micrograms per cubic metre air (µg/m3) in the UK, 20 µg/m3 in the EU and 25 µg/m3 in Australia, all of which exceed the WHO’s recommended limit of 15µg/m3. Therefore, it’s essential for vehicle manufacturers to consider how they can reduce non-exhaust emission through design.
SUSTAINABLE BY DESIGN
When considering how to reduce particulate matter emissions, it’s important for transport manufacturers to consider the factors that determine the production of non-exhaust emissions. Reducing brake wear is the key area for transport manufacturers can concentrate their efforts to reduce emissions thanks to regenerative braking technology.
In regenerative braking, upon deceleration, the vehicle’s kinetic energy is recovered and stored in the vehicle’s battery, increasing EV range and improving energy consumption. However, it’s important that these systems have a safety mechanism in place for when the vehicle’s battery is in a high state of charge. If the battery is full or there is a failure it will be unable to store additional energy from thebraking system. Therefore, the energy must have an alternative pathway to keep the vehicle’s power system functional.
A dynamic braking resistor is an essential component of a regenerative braking system, safeguarding the EV by removing excess energy and dissipating it as heat. Most of the time, electric brakes will be sufficient to slow the vehicle, meaning that the mechanical system will only be used at very low speeds when the motor cannot generate sufficient braking force to stop the vehicle quickly. Less reliance on the brakes leads to minimised brake wear, resulting in a reduction in particulate matter and non-exhaust emissions.
The 2030 ban on petrol and diesel vehicles will ignite the elimination of exhaust emissions, but the idea that this will result in a zero-emission fleet is incorrect. Although some of the contributing factors to non-exhaust emissions may be out of our control, it’s important to minimise those that we can, like vehicle mass and brake wear, to reduce risks for the population and the planet.