WHAT’S STILL HOLDING BACK EV SALES?
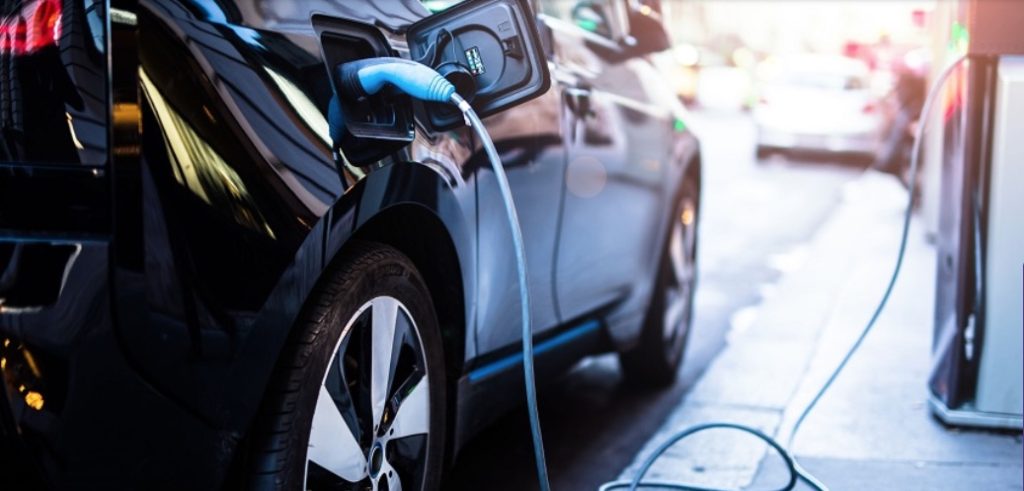
ELECTRIC VEHICLE (EV) UPTAKE IS INCREASING, BUT SOME DRIVERS REMAIN HESITANT
In his 2022 Autumn Statement, Chancellor Jeremy Hunt announced that electric vehicle owners will have to pay road tax from 2025. Critics say the move will further hinder consumers from purchasing an EV sooner than they need to. But, even as EV adoption continues to climb, what are the other reasons holding people back from making the switch?
Though EV uptake has been increasing in recent years, new electric car registrations still lag far behind petrol and diesel vehicles. The Government’s Vehicle Licensing statistics for 2022 showed that in the April to June period, 13 per cent of new car registrations were fully electric, with petrol still taking the majority at 53 per cent. But, when under increasing pressure to meet climate carbon targets, why is there still a reluctance to switch to an electric vehicle?
SURGING ELECTRICiTY COSTS
With energy bills doubling over the past year, the cost of powering an EV is a major barrier to their adoption. A poll by the AA suggested more than three in five drivers have been put off owning or switching to an EV due to skyrocketing electricity costs.
And those who can’t charge their vehicle at home need to pay even more for their electricity. Public chargers can cost up to twice as much, with the RAC Charge Watch reporting a 42 per cent price increase in 2022 for using a public rapid charger.
LACK OF RAPID CHARGERS
According to Zap-Map, out of a total 36,000 public charging points across the UK, only around 7,000 of these are rapid or ultra-rapid chargers. With non-rapid chargers potentially taking several hours or even overnight to charge an EV battery, there’s a very noticeable difference when switching from a petrol or diesel that takes only minutes to refuel and has a much longer range on a single tank.
The charging times of non-rapid chargers can also mean that a charging point is taken up for several hours, unlike a petrol station where each pump is only occupied for minutes. When it comes to electric power, the number of charging points needs to reflect the number of cars as well as their expected recharging times.
UPFRONT COST
Many potential customers are discouraged by the initial cost of an electric vehicle, often considerably higher due to the more expensive technologies used in EVs. Insurance firm LV found new EVs to be an average of £7,000 more expensive than their petrol and diesel equivalents. And this trend follows into the used car market, with a used electric hatchback up to 27 per cent more expensive than its petrol counterpart.
With mounting pressure to reduce carbon emissions on the roads, it’s inevitable that drivers will need to switch to EVs before long. But what can manufacturers do now to help improve the EV uptake?
BOOSTING EV EFFICIENCY
Increasing EV uptake, particularly before the ICE deadline, will require effort from all stakeholders — be that automakers, infrastructure developers and government. When designing EVs, there are several considerations manufacturers can make to boost their efficiency and thus make them more commercially attractive.
One way of boosting vehicle efficiency, which positively contributes to EV driving range, is implementing regenerative braking. This process takes the excess energy generated when the vehicle is braking, and reverses the flow of electricity, putting it back into the battery.
But there may be situations where the energy generated in a sudden burst is too high for the battery to take in, such as when making an emergency stop. This can lead to overvoltages, damaging electrical components within the system, and there are other factors to consider when designing a safe and effective regenerative system.
To dissipate the excess energy safely, resistors should be used. Compact, high power dynamic braking resistors with simple connections are easily installed into existing circuits. Modular resistors can also be put together to match the level of braking power required depending on the type of vehicle.
Though much progress has been made in increasing EV uptake, there are still many drivers who are yet to be persuaded. But we’re not at the end of the road yet, and there are many considerations EV manufacturers can make to make their vehicles a more enjoyable, efficient, and safer drive for end users.